In the case of printed circuit boards (PCBs), the surface finish presents a vital factor in elaborating not only the surface appeal but also the efficiency, durability, and service span of the circuit boards. Choosing the appropriate surface finish is important as it affects the solderability, electrical characteristics, cost, and, in some cases, ecological characteristics. This all-encompassing tutorial is intended to provide information on the different kinds of surface finishes used on PCBs, the advantages and disadvantages of each option, and how to select the most ideal one for your project.
Introduction to PCB Surface Finishes
PCB surface finishes types are a layer that is deposited on the copper of the PCB with the main purpose of protecting the copper from getting an oxide layer on its surface and from soldering. They also help in establishing the parts’ placement and forming secure electrical connections. The type of surface finish to be used depends on some factors like the service conditions, which way the assembly process will be done, the money to be spent, and the time to be taken.
Common Types of PCB Surface Finishes
Here’s a detailed paragraph for each common type of PCB surface finish:
Hot Air Solder Leveling (HASL)
HASL or hot air solder leveling, continues to be preferred as the most common and affordable PCB surface finish with stable performance for a long time. To accomplish this, the PCB is immersed in a solder bath where the component side is coated with molten solder and then de-soldered using hot air knives so that only the copper exposure area is coated with solder. A special merit of HASL is that it offers good-quality solder joints in through-hole components and is rather easy to apply as well. However, it is not recommended for fine-pitch components or surface-mount devices (SMDs) because of the surface it produces, which often interferes with the soldering process by causing solder bridging or insufficient solder joints. Further, due to the processes that happen in HASL, it exposes the PCB to thermal stress, thus affecting its mechanical performance in microelectronics.
2. Electroless Nickel/Immersion Gold (ENIG)
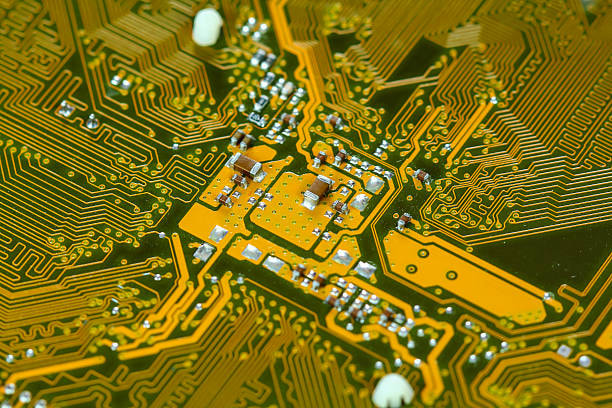
Electroless Nickel/Immersion Gold (ENIG) is preferred for its uniformity and the robust contact during soldering that realizes a level surface finish that is appropriate for SMD and fine-pitch devices. This involves shelpping a layer of electroless nickel on the copper surface of the PCB and then the board is overlaid with a layer immersion gold. ENIG offers better corrosion characteristics and certainly is less vulnerable to oxidation than most of the other finishes. Nevertheless, it is somewhat more expensive than HASL; its problems include black pad defects in which nickel is corroded, which reduces solderability. High-reliability applications, high reliability and constant performance are what ENIG is usually employed in.
3. Immersion Silver (IAg)
Immersion Silver, also known as IAg, is developed by putting a thin layer of silver on the ICL’s copper surface through a chemical displacement process. It provides good electrical conductivity and it can be used in applications that require high frequencies where a signal is important. The solverability of IAg is slightly better than that of ENIG and much cheaper than that of ENIG. However, silver is relatively sensitive to oxidation and hence its reliability can be a problem if not properly treated and preserved. This type of finish has a lower shelf life than most because of issues with oxidation, so it is used in areas where construction and rapid usage are valued more than long-term storage.
4. OSP (Organic Solderability Preservatives)
Organic Solderability Preserver coating or OSP, is a green process that makes use of a water-soluble organic material to help prevent the copper surface to the PCB from getting oxidized. OSP is suitable for soldering, gives a flat surface for mounting and can be used for SMD devices. Hence, it is cheaper as compared to some other finishes, easy to apply and guarantees a smooth surface after application. However, OSP has a short life span; its multifunctional layer is not permanent but only protected by an extra layer, which must be protected from the air during storage and soldering. It also cannot be used in multiple reflow processes or in regions where humidity is high or where chemicals are employed since it is organic and, in time, may degrade.
5. Electroplated Nickel/Gold (ENEPIG)
Electroplated Nickel/Gold (ENEPIG) is a complex surface finish consisting of multiple layers: EN, Pd electroplating, and electroplated gold. This assures good protection against corrosion as well as oxidation, which makes the product suitable for high-reliability applications that would require multiple cycles of assembly and other vicious environments. ENEPIG is suitable for the solderability of both the SMD and the through-hole components and usable for wire bonding processes. Despite this, it has a number of drawbacks, such as being relatively expensive to apply when compared to other types of finishes; it is also thicker than most other finishes and so its application is restricted in thin section work, in projects where thickness control forms a large part of the work and where the processes involved in applying this finish are complex.
Factors to Consider When Choosing a Surface Finish
Environmental Considerations:
- Operating Environment: First of all, one should think about the temperature fluctuations, humidity level, and chemicals or pollutants to which the PCB will be exposed.
- RoHS Compliance: It is especially important to check if the finish of the product must meet RoHS (Restriction of Hazardous Substances) standards if needed.
Assembly Process Compatibility:
- Solderability: Assess to what extent the finish aids in soldering during the assembly method.
- Component Compatibility: Further, the type of component, such as SMD, through-hole, fine-pitch, or the other, has to be thought over concerning compatibility with the finish.
Reliability and Durability:
- Corrosion Resistance: Determine the degree of corrosion protection for the finish in harsh conditions.’
- Mechanical Durability: Think of the effect that mechanical stress can have on it and how the extreme fluctuations in temperature would affect the finish.
Cost and Budget Constraints:
- Initial Cost: Determine the total preliminary cost of the application of the chosen finish and its consequences on the total cost of the project.
- Long-term Cost: It is necessary to notice potential maintenance costs, possible rework connected with the chosen finish, and reliability costs.
Application-Specific Requirements:
- High-Frequency PCBs: Select finishes with low insertion loss and known characteristic impedance.
- High-Reliability Applications: Select these finishes with the highest durability and reliability against the harshest of elements.
How to Choose the Best Surface Finish for Your PCB
- Define Your Requirements: The project documentation must present that project’s needs, the conditions in which it is to be assembled, and any fiscal limitations.
- Evaluate Surface Finish Options: Consider the advantages and disadvantages of each of the surface finish types depending on the established parameters.
- Consult with PCB Fabricators: It is advisable to turn to PCB manufacturers or suppliers for guidance on what they would recommend based on your request.
- Consider Test Runs: Carry out test runs or trials on the various surface finishes on a scale-down model of the actual operating environment.
- Future-Proofing: Also, envision future requirement areas like capacity, availability, and conformance to best practices and legal requirements.
Conclusion
The selection of the most suitable surface finish for PCBs depends on many parameters, including the environmental conditions within which the PCBs will be used, the assembly process, and the costs, among others. All the surface finish types have relative benefits and drawbacks, which means that you should select the appropriate type based on your application needs. Of course, with the knowledge of the particularities and consequences of various forms of surface finish, you will be able to make the right choice—the one that will create maximum effectiveness, durability, and dependability for your printed circuit boards.
To sum up, choosing the surface finish is not only a functional decision but also one that influences the compliance of the PCB with performance requirements throughout its practical use. With this guide, you are ready to make the right choice of PCB surface finish for your project according to the peculiarities of your venture.